Diesel Fuel Quality is a Question not a Guarantee
Diesel engine designs striving to increase engine performance have made great advancements in engine fuel delivery to the combustion chamber. Today’s diesel engine is quieter, smoother, and more powerful. But today’s diesel engine owners are overlooking one important factor. The quality of today’s diesel fuel has not advanced at the same rate as the engine improvements.
In recent years government mandates required a percentage of each gallon of fuel contain some biodiesel. Biodiesel inherently has water in it. Per the ASTM spec D2709 “Water and Sediment”, water volume percentage maximum is 0.05%. Not much, but ask the engine manufacture as to the allowable percentage of water in the engine fuel. They will say ZERO.
Now for the water issue, understand that most fuel has some amount of water in it from either the refining process and addition of biodiesel, rain water enter through vents and hatches, poor transportation practices or bacterial growth. A lot of problems are “delivered to you”.
One short note on condensation. For each cubic meter of air at 100% humidity will produce 22 grams of water. 22 grams is .74 ounces or 1.48 table spoons. Do the math on your tank and calculate the amount of air space and you will see that worst case scenario condensation is not a big deal.
Then there are algae. There are absolutely no algae in diesel fuel. You may have fungus and microbial contamination but no algae. This is a misnomer for diesel sludge that is a bio-mass. So if you have a diagnosis of ALGAE and add a biocide, you have found a mechanic that not as smart as he should be. More follows.
Diesel fuel begins to deteriorate as soon as it is produced. Within 30 days of refining, all diesel fuel regardless of brand, goes through a natural process called re-polymerization and oxidation. This process causes the fuel to darken and over years drop to the bottom of the fuel tank and form asphaltene. The fuel begins to turn dark in color, smell bad, and in most cases causes engines to smoke. Your filters only address the symptom and not the cause.
Why is there so much bad fuel?
There was a time when diesel fuel remained in the refinery storage tanks long enough to naturally separate and settle, allowing the clean fuel to be drawn off. Now with increased demand, diesel fuel never remains stationary long enough for settling, and the suspended water and solids are passed on to you, the user.
This quality issue requires that we realize the added burden placed upon diesel fuel as opposed to gasoline. Gasoline acts as a fuel only. Diesel fuel, on the other hand, also must cool and lubricate injection system parts. These parts are engineered to very close tolerances – up to 0.0002 of an inch – and any contamination means rapid part wear. The smallest amount of water displaces the diesel fuel. When the fuel is displaced wear occur because lubrication is now absent.
Water that enters the combustion chamber results in even more serious damage. When it comes in contact with the heat of the combustion chamber (in excess of 2000 degrees F), it immediately turns to steam and often explodes the tip of the injector. Water causes corrosion of tanks, lines, injectors, and greatly reduces combustibility.
The solution: Multi functional diesel additive packages and hardware.
The improvement of fuel quality by the use of additives and current technology is always a good choice.
Many diesel fuel additive packages address the key issues with respect to fuel performance; some improve fuel economy, increase lubricity, improving cold flow, and improve cetane number.
Most diesel fuel additives contain combustion improvers that release oxygen during the compression stroke. This allows combustion to start sooner, providing for a more complete fuel burn. A more complete burn provides all the power your fuel and engine is capable of producing..
Cetane is a performance rating of a diesel fuel, a higher cetane number or cetane rating indicates greater fuel efficiency. The fuel’s cetane influences, duration of white smoking after start-up, drivability before warm-up, and intensity of diesel knock at idle. Increase the cetane number of a fuel and you have improved performance.
In diesel fuel systems, the fuel provides lubrication for the fuel pump and injectors. A fuel with poor lubricity can cause excessive wear and premature failure of these components. Improve lubricity and extend engine life.
Diesel fuels have pour points (the lowest temperature at which an oil or other liquid will pour under given conditions) within the range of normal winter temperatures. As a fuel approaches its pour point, paraffin in the fuel form wax crystals that prevent it from flowing. Flow-improver additives modify the wax crystals, lowering the pour point of the fuel and give better cold weather performance.
For on-sight storage tanks other issues must be looked at. On-sight storage tanks always have a small amount of the first gallon of fuel ever put in them, unless it is drained 100% and cleaned. So adding new, fresh fuel always has a bit of the bad added to it every time fuel is purchased. Diluting the bad with good over time is a loosing battle. The fuel will always be bad fuel until the core problem is addressed. This applies to you if you store fuel and surly applies to your fuel supplier. An interesting question to ask your fuel supplier is how often do they empty and clean their fuel storage tanks? If seldom or never cleaned, sediment builds up in the bottom of the tank then when tanks are refilled the sediment is stirred up and pumped out with the new product for you to deal with.
One side note on additives and water, many additives claim to dissolve or disperse water so it can be burned off. I have never seen water burn but to give them credit most additive designed to improve performance to show good results. (Dieselcraft’s Technol 403). For large volumes of stored fuel adding a de-emulsifier may take suspended water from the fuel so it can be removed with a mechanical water separator.
The order of treatment for fuel related problems should always begin with a determination of whether there is water in the fuel and if the fuel has microbes (fuel bugs) in it. A Microbe Fuel Test Kits, Dieselcraft DS-1, can be used for this stage of maintenance. Biocides have no effect on and will not eliminate a sludge problem. Biocides only kill bacteria! Sludge dispersant is needed to break up the biomass so the biocide can work.
The water issue should always be remedied first by removing the water from the tanks bottom, by pumping or draining, then the use of fuel water separators on the tank or on the equipment. A chemical additive should be added to improve fuel stability. For long-term prevention, on a regular basis circulate and filter the fuel. This is known as Fuel Polishing. This will continually reverse the re-polymerization of the fuel during circulation and reduce the need for ongoing additive use.
Conclusion
Eight out of every ten diesel engine failures are directly related to poor quality and contaminated fuel. The build-up of contaminates in the fuel systems and storage tanks can quickly clog filters, thus resulting in engine shut down, fuel pump wear, and engine damage.
There is no good time to find out that your engine won’t operate because of contaminated or poor quality diesel fuel. Since no one can predict a breakdown, the only safe method is prevention.
Realize now that you do have a problem, and manage it now, or deal with the unexpected catastrophe and reduced equipment life that comes at the absolutely wrong time and is not in the budget!
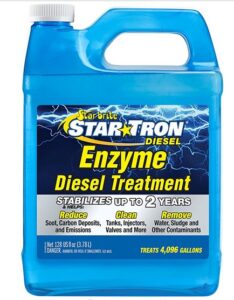
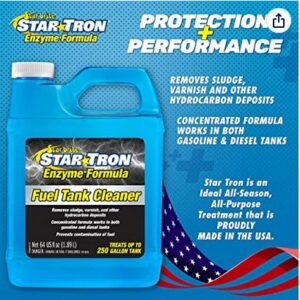
Recent Comments